This article may contain references to products or services from one or more of our advertisers or partners. We may receive compensation when you click on links to those products or services. Nonetheless, our opinions are our own.
The information presented in this article is accurate to the best of our knowledge at the time of publication. However, information is subject to change, and no guarantees are made about the continued accuracy or completeness of this content after its publication date.
Key Highlights
- Holding costs include all the money spent on keeping unsold inventory. This covers storage, insurance, labor, depreciation, and lost opportunities.
- These costs usually make up 20-30% of the total inventory value, so they are important in inventory management and supply chain work.
- Knowing about holding costs helps businesses keep the right inventory levels, handle dead stock, and ensure good cash flow.
- To figure out holding costs, you should list the related costs, collect financial data, and use a clear formula.
- Ways to lower holding costs effectively include making warehouses work better, using technology, and predicting demand accurately.
Introduction
Have you ever considered how the costs of holding unsold inventory impact your business? Holding costs matter for managing inventory. They influence how well your supply chain operates and how much profit you earn. These costs include fees for storage space, the loss of inventory value, and lost business opportunities. By understanding holding costs, you can sell your inventory faster, manage your cash flow better, and make smarter financial decisions. Let’s explore holding costs, their different types, and how to calculate and lower them. This can help improve your financial health.
Understanding Holding Costs
Managing inventory is about balancing various costs. One major cost is holding costs. These costs happen because of storing unsold inventory. They also include losses in value and lost opportunities. For businesses, holding costs are unavoidable expenses. They can have a big impact on profits.
When inventory sits in storage for a long time, costs go up. This can hurt cash flow. That’s why it is important to understand these costs. Doing so helps in making plans that improve supply chains, avoid dead stock, and make inventory storage more efficient.
Definition and Importance
Holding costs, also known as carrying costs, are the total costs of keeping inventory before it is sold. These costs cover real expenses like warehouse space and employee pay. They also include hidden costs such as loss of inventory value and lost chances. Understanding these costs is key to calculating the economic order quantity. This helps determine the best time to reorder inventory.
Tracking holding costs is important because they impact profits. High holding costs can lower cash flow and increase the cost of inventory. This can eat into profit margins. To save money, you should regularly review these costs.
Inventory turnover shows how quickly stock moves through your supply chain. It relates to holding costs. A higher turnover rate means shorter storage times. This helps to reduce carrying costs. When businesses align inventory management with customer demand, they can maintain the right amount of stock and manage their costs well.
Common Types of Holding Costs
Holding costs are made up of several parts that contribute to total inventory expenses. These parts include tangible costs, intangible costs, and unexpected losses.
- Storage Costs: These are what you pay for renting space in a warehouse, utilities, and insurance to keep your inventory safe. If you manage the space well, you can lower these costs.
- Safety Stock Costs: Having extra stock can help meet customer demand. However, it can also raise costs that impact your cash flow.
- Dead Stock: This is inventory that you cannot sell or is no longer good to sell. It takes up space and means lost money. Finding ways to use or sell dead stock can help cut down on financial losses.
- Opportunity Costs: These are the potential losses from keeping unsold inventory instead of using that money for other investments.
Understanding these costs helps you solve issues in your warehousing and inventory systems. This knowledge can also boost your cash flow management.
Voted "Best Overall Budgeting App" by Forbes and WSJ
Monarch Money helps you budget, track spending, set goals, and plan your financial future—all in one app.
Get 50% OFF your first year with code MONARCHVIP
Preparing for Holding Cost Calculations
Before you start any calculations, it’s key to prepare properly. First, determine the costs that are most important to your total inventory expenses. This first step helps you understand how you spend your resources.
Using past sales and financial reports makes this process simpler. Today, inventory management tools can help you track your inventory costs month by month. They can also show you areas for improvement. When you plan, your calculations will be more precise. This also gives you good ideas on how to lower holding costs effectively.
Essential Tools and Resources Needed
Having the right tools helps you figure out holding costs easily and keeps things accurate. An inventory management system is essential. It tracks stock movement, costs, and turnover in real-time.
Accessing past sales data helps us understand buying trends. This information is useful for managing safety stock and improving demand forecasts. It also lowers risks, such as having too much inventory.
You need all the financial data to see costs like storage, pay for workers, and loss of value over time. Using these tools together helps you understand your supply chain better. It also points out places where you can save money.
Basic Financial Terms and Principles
Understanding basic finance is key to knowing holding costs. The cost of inventory covers both fixed and variable costs. These costs arise from several steps, including obtaining goods, making them, and storing them for the first time.
Capital costs are the funds required to purchase inventory. This includes materials and any additional costs, such as loan fees. These costs impact the amount of working capital your business uses.
Opportunity cost is a cost that is not always clear. It refers to the money you might lose if you keep unsold inventory. When businesses lower opportunity costs, they can use their resources more wisely. This allows them to focus on projects that can make more money, resulting in better cash flow.
Step-by-Step Guide to Calculate Holding Costs
Calculating holding costs is simple if you understand how to do it. First, write down all the costs related to storing and managing your inventory. This will help ensure you don’t overlook anything important.
Once you have your data, put the numbers into the inventory holding cost formula. Looking at the results will help you see where you can improve. This helps you with operations and reduce waste. Keep reading for more steps to get the right calculations.
Step 1: Identify Relevant Costs
The first step to understanding holding costs is to find the key inventory expenses. Start by listing the main costs. These costs include storage fees, employee wages, and utilities for the warehouse.
Next, think about the costs that are harder to measure. These costs include depreciation and missed opportunities. They can be tricky to figure out, but they are very important for your final amount. For instance, having dead stock can prevent you from investing in products that could earn you more money.
Finally, add these costs to your total inventory costs. This way of organizing helps you calculate easily and shows you where your money is going.
Step 2: Gather Financial Data
Getting the right financial data is important for figuring out holding costs. You need to go to the county assessor’s office to learn about property taxes for storage facilities. These costs directly impact carrying charges.
You should also watch out for costs in real estate, like insurance payments and storage rental fees. Writing down your monthly and yearly expenses is a smart practice. Consider using financial management tools to keep everything accurate.
Using your business’s past financial data allows you to see earlier inventory costs. This enables you to compare today’s expenses. You can then adjust your forecasts to better control future holding costs.
Step 3: Use the Holding Cost Formula
To find out the holding costs, just use this easy formula:
Inventory holding cost is found by adding storage costs, employee salaries, opportunity costs, and depreciation costs. Then, divide this total by the total value of the annual inventory.*
First, add together all costs, both direct and indirect. This includes storage fees, employee wages, and how much the inventory loses value over time. These costs are very important for the formula.
Next, add up all these costs. Then, divide that total by the total value of your annual inventory. This will give you your holding cost. This percentage shows how well you are using your resources.
Step 4: Analyze the Results
Looking at holding cost results can help you see how well your finances are doing. Find the categories that cost a lot and check the inventory levels. This will help you understand how you use storage space and how quickly products sell.
Use a text table to summarize findings clearly:
Category | Expense ($) | Percentage of Total Cost (%) |
---|---|---|
Storage Costs | 20,000 | 40 |
Opportunity Costs | 15,000 | 30 |
Depreciation Costs | 10,000 | 20 |
Employee Costs | 5,000 | 10 |
Looking at the table allows businesses to find ways to get better. They can make changes like adjusting stock or improving the warehouse layout to be more efficient.
Strategies to Reduce Holding Costs
Using smart strategies can lower holding costs. Start by improving your inventory levels. Make sure your stock matches customer demand. This will help you avoid dead stock while having enough safety stock.
Also, make warehouse operations better. Use space wisely and improve the way you fill orders. This can help lower costs. Always consider using technology, such as inventory management systems, to keep track of numbers and automate tasks. Taking these steps can help you spend money more wisely.
Optimizing Inventory Levels
Good inventory management is about having just the right amount of safety stock. It is important to avoid having too much. This practice prevents dead stock from building up. By figuring out how much to order, businesses can meet customer demand better.
Finding better ways to predict inventory levels can remove uncertainty from the process. By reviewing past sales and trends, we can make more accurate stock predictions. This will lower the risk of taking up too much warehouse space.
By improving inventory turnover, businesses can save on holding costs. When products sell quickly, they spend less time in storage, which helps control expenses over time.
Enhancing Warehouse Operations
Operational efficiency is key in warehouses. It helps reduce holding costs. When you use organized racking systems for inventory storage, it allows you to make the best use of available space.
Outsourcing storage to fulfillment centers can lower fixed costs. These centers take care of inventory and provide services such as picking, packing, and shipping.
Using automated inventory tracking systems makes work less complicated and reduces human errors. These systems allow you to view your supply chain clearly. As a result, you get better costs and improved business performance.
Conclusion
In summary, managing holding costs is key for a healthy financial insight. When you understand what impacts these costs and apply effective ways to manage them, your profits can rise significantly. A good method to reduce holding costs is by optimizing your inventory levels and enhancing your warehouse operations. The more often you review and adjust your expenses, the easier it will be to maintain stable finances. If you have any questions or need help with holding cost calculations, don’t hesitate to seek expert advice.
Frequently Asked Questions
What are typical rates for holding costs?
Holding costs often account for about 20% to 30% of your total inventory value. These costs cover storage space costs, labor fees, property taxes, and rental property insurance. The rates may differ depending on the warehouse’s location, the type of inventory you have, and the services needed for your storage.
How often should a holding cost analysis be performed?
You should do a holding cost analysis each year or whenever there is a big change in customer demand. Regular financial checks give you a clear look at your inventory. This helps you keep the right amount of stock and manage costs well. Businesses can improve by adjusting their strategies to fit market changes.
Can technology reduce holding costs?
Yes, technology can greatly reduce holding costs. A good inventory management system makes things easier. It provides real-time data and keeps track of inventory levels. It also automates many tasks. These improvements can save money and increase the productivity of warehouses and inventory.

Reviewed and edited by Albert Fang.
See a typo or want to suggest an edit/revision to the content? Use the contact us form to provide feedback.
At FangWallet, we value editorial integrity and open collaboration in curating quality content for readers to enjoy. Much appreciated for the assist.
Did you like our article and find it insightful? We encourage sharing the article link with family and friends to benefit as well - better yet, sharing on social media. Thank you for the support! 🍉
Article Title: Holding Costs: A Quick Guide to Keeping Your Finances in Check
https://fangwallet.com/2025/05/10/holding-costs/
The FangWallet Promise
FangWallet is an editorially independent resource - founded on breaking down challenging financial concepts for anyone to understand since 2014. While we adhere to editorial integrity, note that this post may contain references to products from our partners.
The FangWallet promise is always to have your best interest in mind and be transparent and honest about the financial picture.
Become an Insider
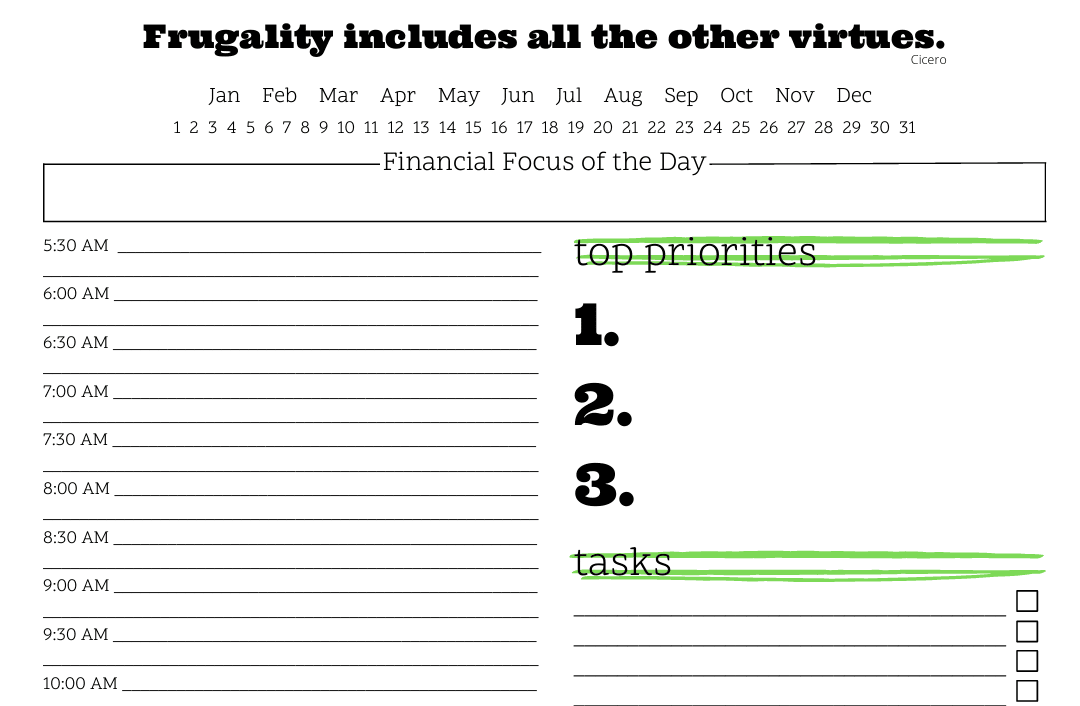
Subscribe to get a free daily budget planner printable to help get your money on track!
Make passive money the right way. No spam.
Editorial Disclaimer: The editorial content on this page is not provided by any of the companies mentioned. The opinions expressed here are the author's alone.
The content of this website is for informational purposes only and does not represent investment advice, or an offer or solicitation to buy or sell any security, investment, or product. Investors are encouraged to do their own due diligence, and, if necessary, consult professional advising before making any investment decisions. Investing involves a high degree of risk, and financial losses may occur including the potential loss of principal.
Source Citation References:
+ Inspo
There are no additional citations or references to note for this article at this time.